Polymer fibers in concrete environment for the Mining Industry in South Africa
Normal short polymer fibers are resistant and durable in the concrete environment. For applications where only reinforcement against shrinkage, and in particular plastic shrinkage, is asked for, as in
sprayed concrete repair, polymer fibers are well suited. They are very efficient at distributing micro-cracks during the plastic phase of hardening and they also help to reduce rebound in wet-mix spraying. In addition, polymer fibers have a positive influence in fire scenarios as they reduce concrete spalling.
Recently, a new type of polymer fiber has been developed. These structural polymer fibers (SP fibers) are more similar to steel fibers in terms of shape and length. They are produced from high quality materials and typically delivered in lengths of 30 to 50 mm. Many test results and applications in Australia, Canada, South Africa, Norway and other European countries have shown that this type of fiber can reach adequate toughness if dosed in the range of 5 to 10 kg/m3. Tests with this dosage range show that SP fibers can reach approximately 900 to 1,200 Joules according to the EFNARC panel test (600 mm square and 100 mm thick panel). Here, energy absorbed in Joules up to a deflection of 25 mm is the standard performance criteria used. This result is more or less equal to the result achieved with 30 to 40 kg/m3 of high quality steel fibers.
These new SP fibers are already widely used in the mining industry around the world and are now increasingly utilized in sprayed concrete linings in tunneling. BASF promotes its fibers under the names of MasterFiber SP 530 / SP 540 / SP 550 (fiber lengths 30 mm, 40 mm, and 50 mm, respectively) and MasterFiber SP 640 / SP 650 / SP 665 (fiber lengths 40 mm, 50 mm, and 65 mm, respectively).
Figure 3-46: Example of structural polymer fibers as used for reinforcement of sprayed concrete linings
The results from a comparison EFNARC panel test made with Novotex 0730 steel fibers (dosage 65 kg/m3) and MasterFiber SP 550 fibers (dosage 9 kg/m3) are shown in the following Table 3-17. Identical mix design, w/c ratio, spraying equipment, nozzleman and accelerator type were used for all three mixes (Mix 1 using setting accelerator MasterRoc SA 160, Mixes 2 and 3 using setting accelerator MasterRoc SA 170). All panels were stored under identical curing conditions.
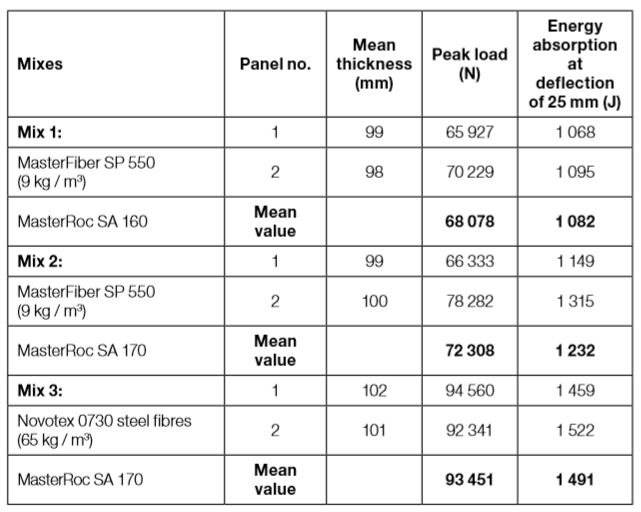
Table 3-17: Results from a comparison panel test (EFNARC) made with Novotex 0730 steel fibers (dosage 65 kg/m3) and MasterFiber SP 550 fibers (dosage 9 kg/m3)
The test results above show that, at a maximum deflection of 25 mm, steel fiber reinforced concrete can only absorb higher energy than concrete at a very high dosage of steel fibers (65 kg/m3) with a standard dosage of SP fibers (9 kg/m3).
The Round Determinate Panel (RDP) test was introduced in 2001. Here, the calculated energy absorption at a deflection of 40 mm is reported as the standard assessment. As reported in [54], RDP and EFNARC panel test results are usually compared at a set deflection (40 mm and 25 mm respectively). While two fibers may have equal performance at these deflections, they may differ significantly at lower or higher deflections. Usually SP fibers work well at higher deflections, while steel fibers work better at lower deflections (see Figure 3-47).
Figure 3-47: Performance as a function of deflection [54]
According to the results of the round panel test shown above, at medium deflections (20 - 40 mm) SP fibers give the same toughness as steel fibers at economic dosages. At higher deflections (greater than 40 mm), steel fibers cease to carry load, while SP fibers continue to absorb load. Thus, SP fiber is the most appropriate solution in situations where there are excessive ground movements, e.g. seismic conditions, rock bursts, high overburden [54].
Further advantages of new SP fibers over steel fibers in sprayed concrete include:
- If corrosion is a concern in cracked sections, the use of SP fibers might be the best option if creep is manageable.
- Reduced fiber-rebound rates.
- Easier logistics and handling.
- Lower wear and tear on spraying parts (wear plate, pump cylinders, inside of pump, hoses and nozzle).
- More economical than steel fibers at medium deflections (20 - 40 mm).
The most common argument against the use of SP fibers in civil tunnel linings is concern about the magnitude of creep-related deflections likely to occur in the long term under gravity loading. The creep behavior of SP fibers and of steel fibers (steel fibers are also subject to creeping!) has been studied by Dr Stefan Bernhard in a long-term investigation program. The test is described in his paper [47], where he concludes that:
“SP fibres are designed and have been shown to provide similar resistance to load deformation as steel fibres. Creep only becomes an issue if and when the sprayed concrete cracks. If a crack develops in steel fibre reinforced concrete, it creates the opportunity for corrosion and loss of performance in ductility. If the load continues, the load energy will continue to be absorbed, but there is a risk of sudden rupture. If a crack develops in SP fibre reinforced concrete there is no corrosion risk. If the load continues, the fibres will stretch rather than suddenly fail, and in doing so will continue to absorb the load energy. The cracked sprayed concrete can be observed and action taken to remedy the cause of the problem before this capability is exhausted”.
In the following Table 3-18 the results from a comparison test made with Enduro SP fibers in three different dosages (5, 7, and 9 kg/m3) is presented. Identical mix design, accelerator (MasterRoc® SA 162) and spraying equipment (manipulator) were used for all three mixes. The toughness test was performed according to the EFNARC panel test.
Table 3-18: Results from a comparison test made with Enduro SP fibers in three different dosages. Toughness test performed according to the EFNARC panel test.
A combination of normal/short (fibrin) polymer fibers with the new SP fibers is probably the ideal reinforcement for sprayed concrete in terms of mechanical performance (reduction of plastic shrinkage, improved bond, reduced spalling during a fire, improved ductility/load bearing capacity) and economical advantages (less cost per m3 applied, improved durability).
Design aspects
Fiber reinforcement shall be specified preferably by the performance requirements of FRSC or alternatively by the type and amount of fibers in the concrete mix. The performance of FRSC can be characterized by means of different test methods according to European, Japanese and American Standards, and more recently by a method developed in Australia. Performance is checked through these tests by measuring the ability of FRSC to carry loads in flexure beyond the flexural capacity of the concrete itself, i.e. ductility / toughness.
Design guidelines for steel-fiber reinforced concrete (SFRC) that made use of a stress-strain relation were first developed by the German Concrete Society ‘Deutsche Beton- und Bautechnik-Verein E.V.’ (latest publication ‘DBV-Merkblatt Stahlfaserbeton’, October 2001), and later on by RILEM (‘Final recommendation of RILEM TC 162-TDF: Test and design methods for steel fibre reinforced concrete’). The project designer should specify the performance requirements for fiber-reinforced sprayed concrete. The toughness of concrete is specified by the residual strength or by the energy absorption capacity of the FRSC, which can be estimated by the load deflection curve from a beam or plate test.
In many cases, fibers are specified to reduce the amount and spacing of bar reinforcement or to avoid its use completely. The latter requires specification of construction joints in the design, since the overlapping of fibers is not possible at construction joints (e.g. between crown, bench and invert), and conventional reinforcement, mostly by means of welded wire meshes, has to be installed additionally.
Regarding the mixture proportions of fiber-reinforced sprayed concrete, different types of fiber usually require different addition rates, since fibers differ in material, length and shape. These should be recommended by the suppliers of fibers and then confirmed by trial tests. The quantity of fibers rebounding, and hence the final amount of fibers in the sprayed concrete, is affected by changes in the quality of the fresh concrete. For the same post-crack performance, fiber dosages in the wet-mix process are sometimes lower than in the dry-mix process, because the rebound of macrofibers in wet-mix sprayed concrete is typically less than for dry-mix sprayed concrete.
The normal materials used in sprayed concrete are used in FRSC. Cementitious materials such as silica fume, slag, and fly ash are frequently added to the concrete mix. For overhead and vertical placement with microfibers, these additional materials can help the construction of thicker layers without sloughing and reduce fiber rebound. For FRSC with more than 0.3% by volume of fibers, water-reducing admixtures are usually added to the mix to maintain the required ratios of water to cementitious materials.
The addition of fibers may affect the pumpability of sprayed concrete. Therefore, mix design and admixture selection have to be adjusted accordingly. Fibers shall be stored according to the supplier’s recommendations.