Concrete Riding Shotgun
Mark Bury
Master Builders Solutions US & Canada
My adventurous side has gotten me outside my comfort zone many times. I have raced motorcycles, navigated class 6 whitewater, parachuted out of an airplane and ridden my motorcycle on a 2,000-mile (3,220-kilometer) road trip over a weekend. It is in that spirt that I contemplated driving from the Atlantic Ocean to the Pacific Ocean, for this adventure.
But wait, another adventurous thought popped into my head! Why not involve my work with concrete? If you didn't already know, concrete is a perishable material, and due to a chemical reaction when water is added, it begins to harden rather quickly, and would not typically be driven great distances. Taking a cross country trip with fluid concrete riding “shot gun" was probably outside of anyone's comfort zone. For this long distance trip with fluid concrete I am using a stabilizing concrete admixture, MasterSet® DELVO, that temporarily stops the chemical reaction from occurring, allowing the concrete to remain plastic (fluid) for the duration of my 7-day trip. At least that was my hypothesis that I was going to prove. This trip will certainly set a record for the longest concrete haul in miles and in time. Put on your seat belt and come along for the ride for the next seven days, with me and my concrete companion riding shotgun.
Day 1
I started my trip in the easternmost city of the continental U.S., Eastport, ME, on the Bay of Fundy. Worth a visit, even though it took all day to get there from Cleveland, OH. My first night was at the Motel East where my concrete making materials and equipment were waiting for me. My plan was to make the concrete first thing in the morning, stabilize it, load it into my hybrid SUV, and head to Boston as the first stop on my trip west. But first, I headed to dinner at the Happy Crab and figured a cup of chowder would be the best way to start my coast-to-coast adventure. The quiet, chilly evening with the sun going down earlier than expected is a clear indication that fall is right around the corner.
Fun Fact: The Bay of Fundy is known for having the highest tidal range in the world.
Day 2
It's 5:00 am as I start the power drill and began mixing the concrete in eight, 5-gal pails. The concrete was mixed to a fluid consistency and contained the MasterSet DELVO stabilizing admixture to put it to sleep - what we call it when delaying the hardening process. A few early risers glanced in my direction in the parking lot with very puzzled looks as the drill buzzed away. More later about my humorous interactions along the way. I measured the concrete fluidity with a mini slump cone and took the concrete temperature, as this was somewhat of a science experiment after all. And to have some fun, I put a face on one of the pails of concrete, nicknamed her “Concrete Connie" and seat-belted her in the front seat to ride shotgun while the other pails rode in the back. After setting the odometer and taking several photos, “we" were off to Boston. The Wayside Inn, later called Longfellow's after the poet, was America's first inn, and was my first stop for some lunch. After lunch, I checked the concrete and it was still fluid 6 hours after batching, already surpassing a typical flowing concrete shelf life. So far so good and only another 3,750 (6,035 kilometers) miles to go! The day ended with me pulling into the hotel in Seneca Falls, NY, following an I-90 route to the west coast. In total a 12-hour driving day.
Fun Fact: The Wayside Inn was founded by one of my long past relatives of the Howe family. Pretty cool history and I’m glad that I was able to have lunch at such a historic place knowing it was part of my family’s past.
Day 3
It's 5 am and a quick check of the concrete indicated it was much stiffer than I had expected. Upon further investigation, I determined that the solid ingredients had settled to the bottom of the pail due to 12 hours of vibration during the drive. I used the drill mixer and returned the concrete to its original homogeneous and fluid state! The early learning from the first day of travel was to mix the concrete and take the temperature daily. If the concrete was traveling in a ready-mix truck, the constant slow rotation of the drum would help the concrete to remain homogenous. Keeping concrete fluid for an extended period in the real world has several benefits. One of which is that it allows concrete producers to batch and deliver concrete to remote locations in lakes and oceans where it takes several hours to transport the concrete to projects by barge/boat or in the middle of the desert, without the fear of it setting up (hardening) or in long distance pumping applications such as underground construction. It's also beneficial in the event of a rain delay, construction delay or lengthy traffic situation. Today's plan is to follow I-90 West through Rochester, Buffalo, and Erie with a quick stop in Cleveland, my hometown.
Many Master Builders Solutions products were used in building structures in downtown Cleveland, such as the Rock and Roll Hall of Fame and Museum, Progressive Field (home of the Cleveland Guardians), Cleveland Browns Stadium (Cleveland Browns), the Great Lakes Science Center, and the Key Center. If you visit the Great Lakes Science Center in Cleveland, you may see the rotating display containing the first concrete to be mixed in outer space aboard the space shuttle Endeavour, mission STS 68, donated by Master Builders Solutions. After another long driving day, I spent the night in Portage, IN.
Not so fun fact: If concrete hardens inside a full ready-mix truck, it is extremely problematic and almost impossible to get the concrete out and the drum is quite likely a loss, a very expensive loss.
Fun Fact: The Key tower, 57 stories (947 ft [288 m]), is the tallest structure between Philadelphia and Chicago. The concrete in the tower was optimized to make the tower very strong and rigid. The reason behind this is that engineers have determined that less rigid towers tend to sway at the top causing inhabitants to get nauseous on windy days. Newer skyscrapers are designed using concrete that is much more rigid to minimize this effect.
Day 4
Upon leaving Portage IN with “Concrete Connie," it is much cooler than the previous few days. It was overcast and about 66OF (19OC). Next on to Chicago, where traffic was, as expected, causing quite a delay, much like the traffic that can be experienced by ready-mix trucks on the way to a job. There was no time to stop for sightseeing, but it was easy to see the Willis Tower, formerly the tallest building in the world, now the 3rd tallest in North America.
The rain started to get heavy as I headed north thru Wisconsin, Minnesota and into South Dakota. This was a tough stretch of driving with only a few windmill farms to provide some scenery. While driving over 700 miles (1,127 kilometers) to Rapid City South Dakota on a two-lane concrete interstate, I had to do the math. Let's see, for a 12 ft (3.7 m) wide left lane, a 12 ft (3.7 m) wide right lane, a 4 ft (1.2 m) left shoulder and a 10 ft (3.1 m) right shoulder and concrete 12 inches (305 mm) deep (common for interstates), then that stretch of interstate would have required over 5,000,000 yd3 (3,822,774 m3) of concrete – in one direction. Wow that's a lot of concrete! Over 10,000,000 yd3 (7,645,549 m3) if you include the eastbound interstate. After arriving in Mitchell, I had a quick dinner, mixed the concrete with the mixer and went to bed.
Fun Fact: Master Builders Solutions supplied concrete products and expertise when the Willis Tower (a.k.a. Sears Tower) was built in the early 70's. Willis Tower is a 110 story (1,451 ft [442 m]) skyscraper in the Loop area of Chicago.
Day 5
Even with a time change 5:00 am comes pretty fast after several long days of driving. Briefly mixing the concrete and taking its temperature before setting out was now routine. The highlight of this day would be Mount Rushmore. “Concrete Connie," was still riding shotgun and fresh as can be. At Mount Rushmore she wanted to get a close up view of that incredible piece of sculpting. I took several photos of her at Mount Rushmore where the busts of George Washington, Thomas Jefferson, Theodore Roosevelt, and Abraham Lincoln were carved into the granite stone. Surprisingly, “Concrete Connie" was so popular that others wanted to get their picture taken with her, so I spent some time taking photos of her and tourists from all over the world.
But I also had a surprise waiting for “Concrete Connie." In the Mount Rushmore photo, you can see all of the aggregate pieces chiseled from the mountain below the sculpted faces. This is the area where “Concrete Connie's" two sisters, “Sandy" and “Aggie" met up with us for the duration of the journey to California. It is a long drive to Denver, CO from Keystone, SD (about 375 miles [604 kilometers)) which is my anticipated stay. The temperature was around 80 OF (26.7 OC) as I passed through Cheyenne, WY on the way to Denver. I took Connie, Sandy, and Aggie to the Denver International Airport to see the simulated snow-capped mountains on top of the airport terminal. The Denver International Airport is quite a concrete structure. It hosts the longest commercial runways in the U.S. - the only commercial runway long enough to land the space shuttle! Another 14-hour day coming to a close as tomorrow's leg is shaping up to be a long one.
Fun Fact: Granite is a very common rock used as coarse aggregate in the manufacturing of concrete.
Fun Fact: Master Builders Solutions spent several years working with several local concrete producers who provided the concrete for this airport. The concrete had multiple durability-enhancing additives to make the concrete last longer.
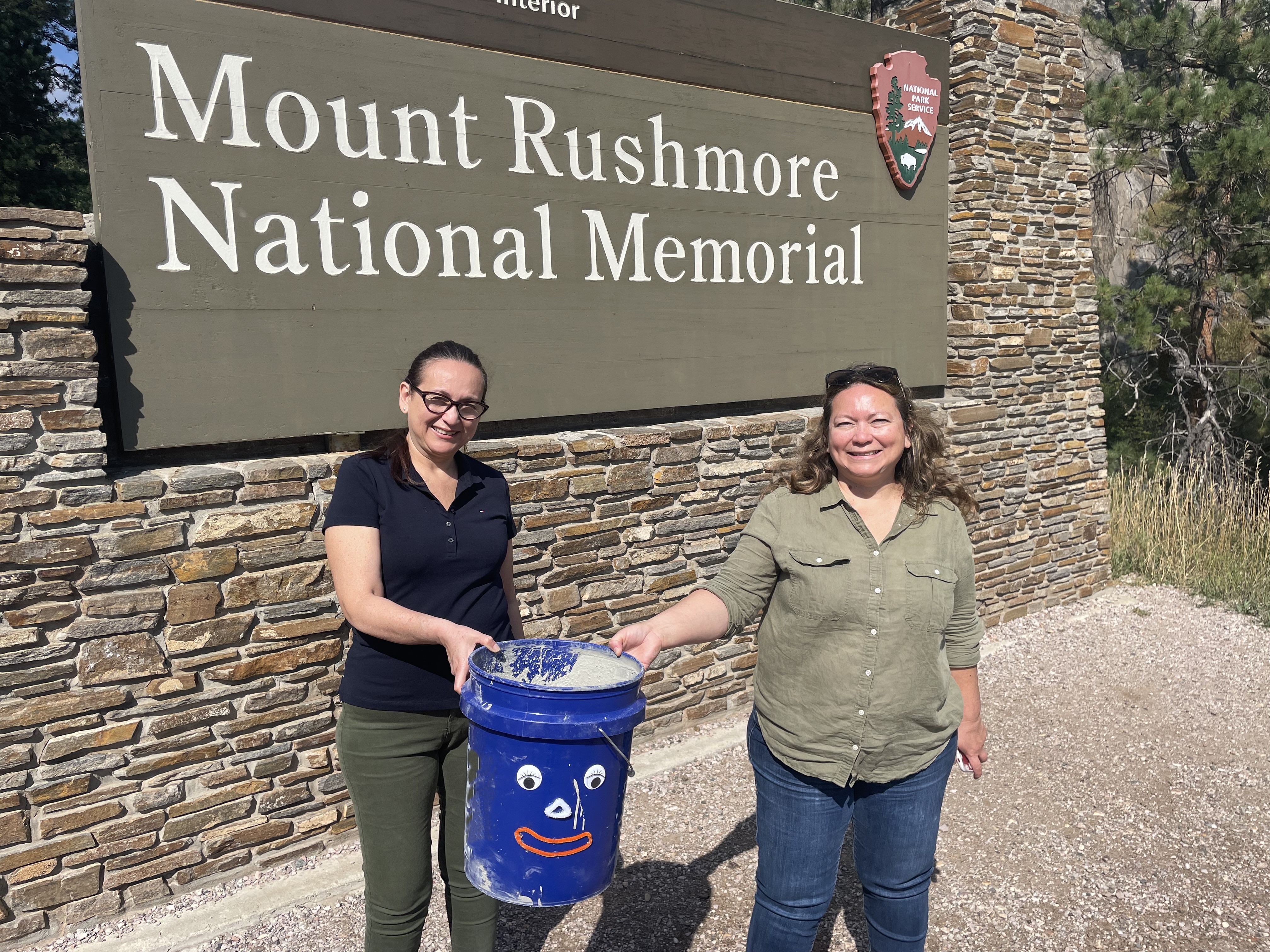
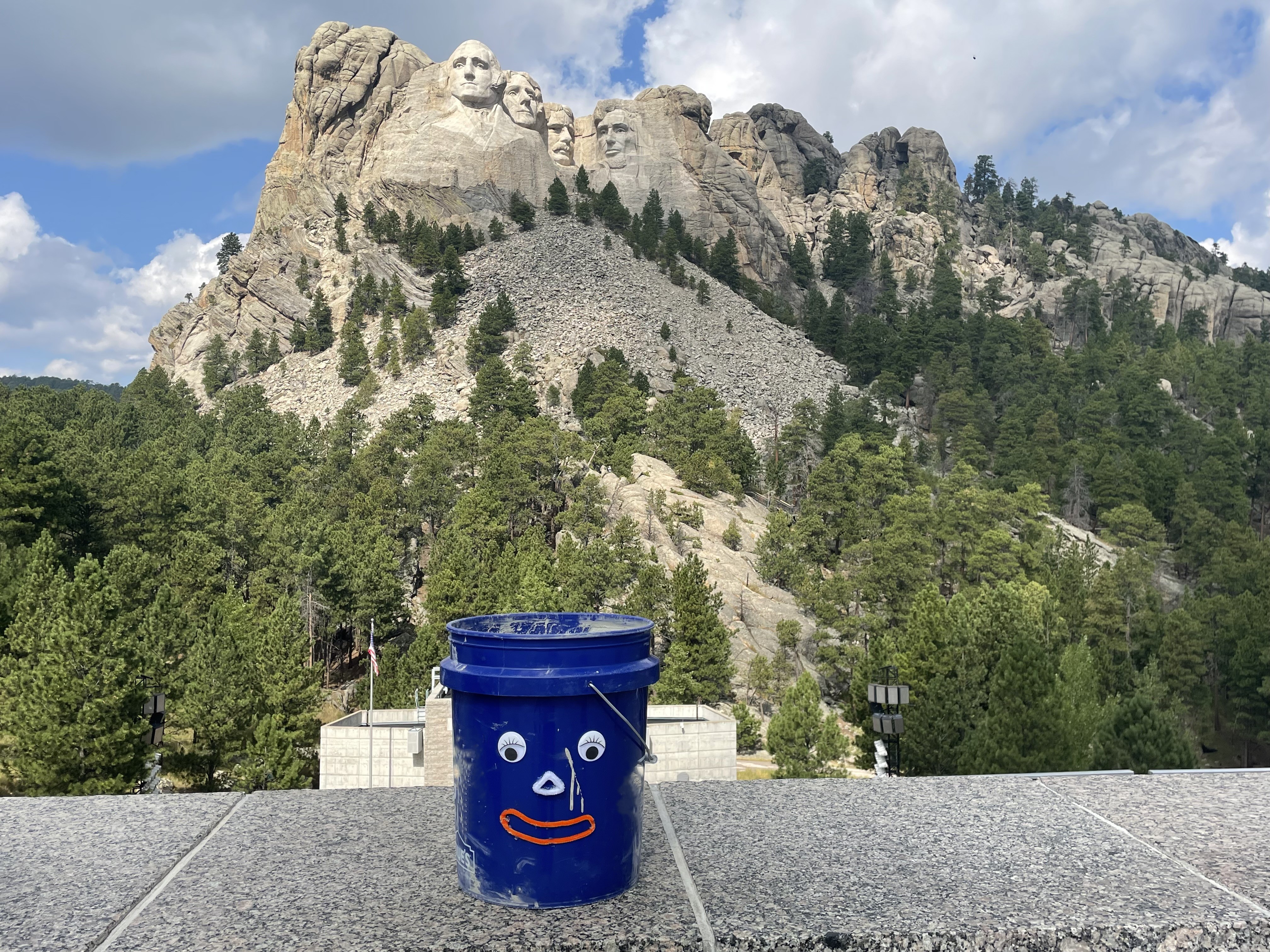
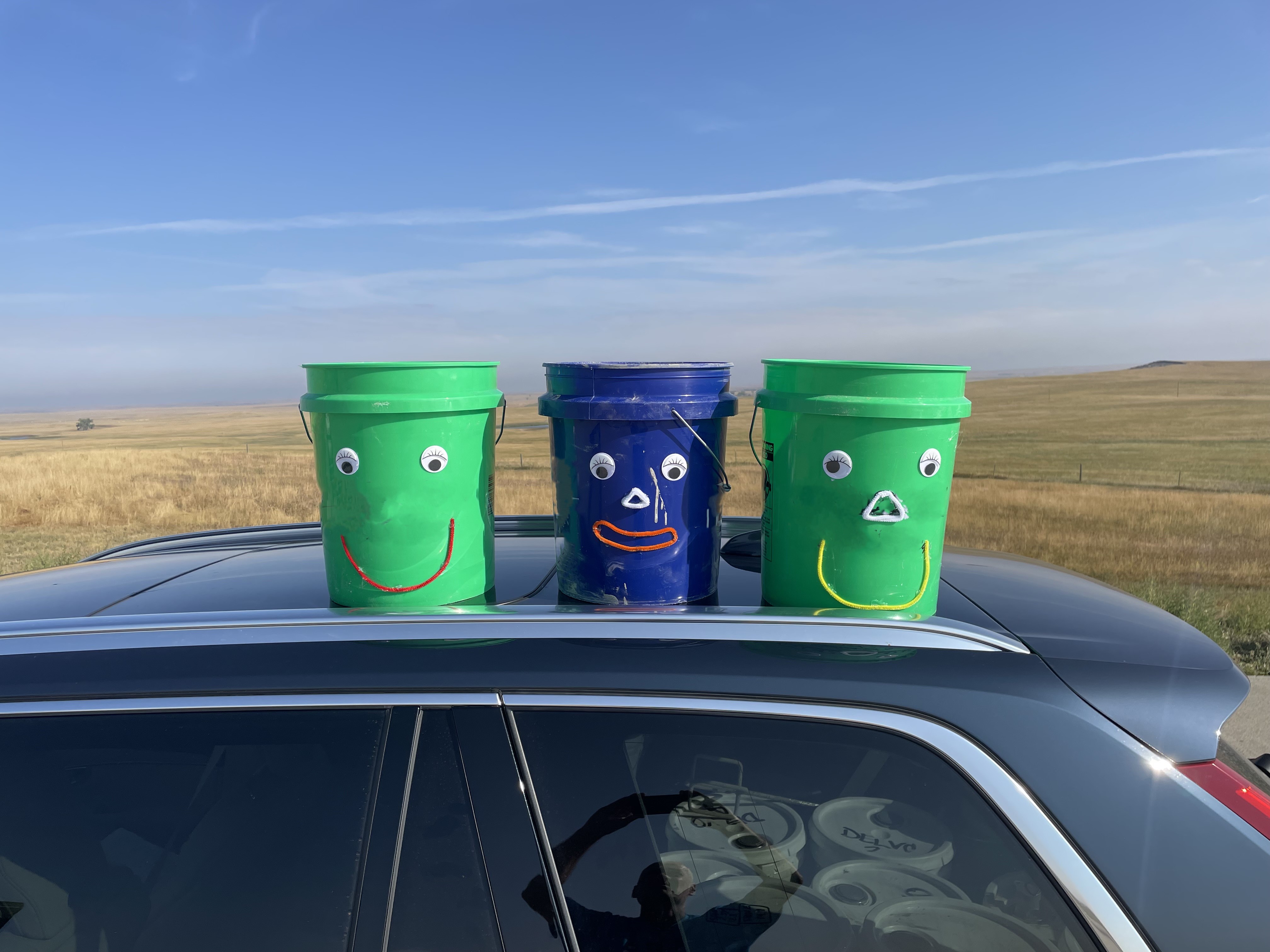
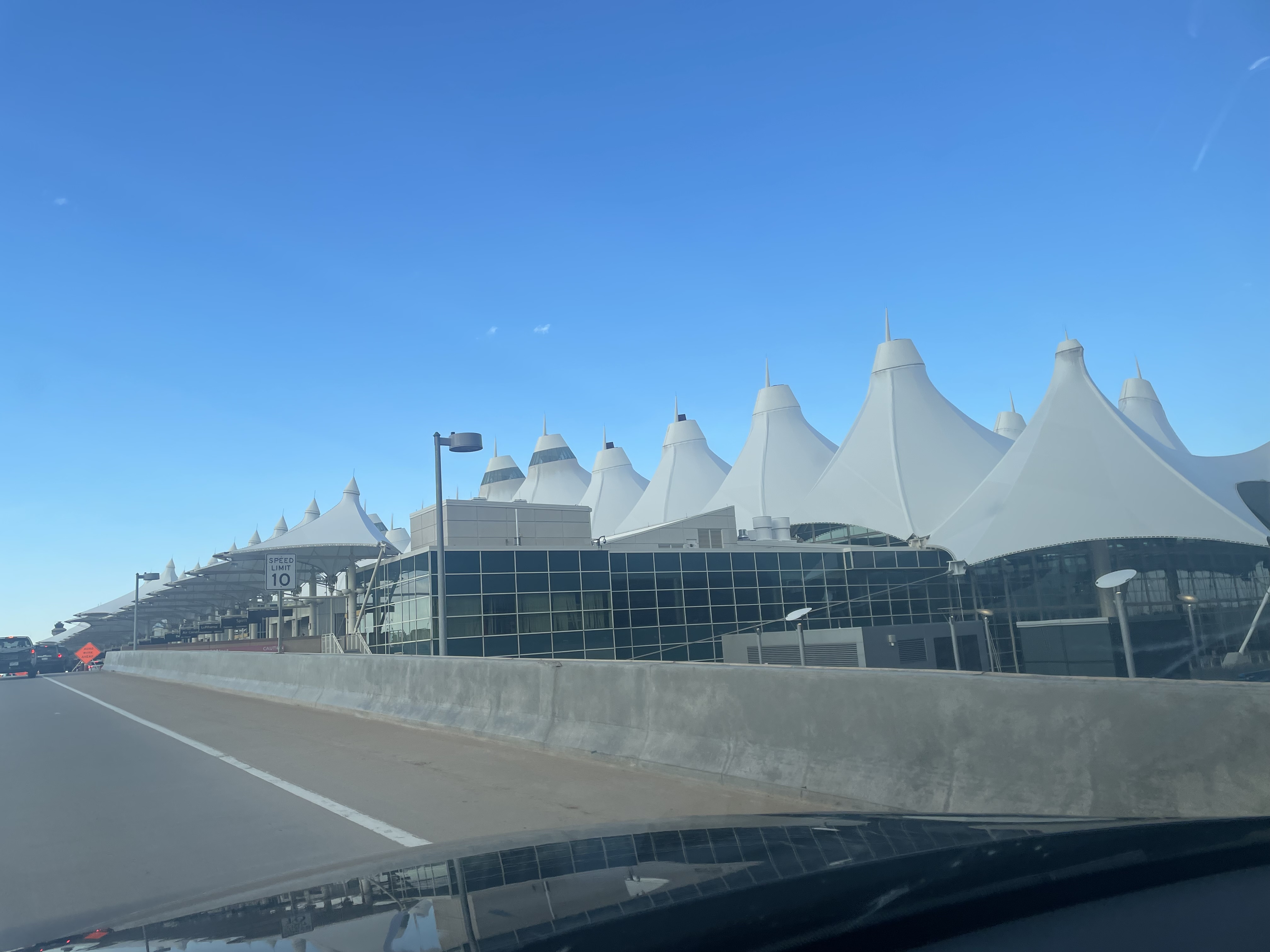
Day 6
Today is starting at 4:00 am as I am giving all eight buckets of concrete a stir with the mixer in preparation for the ~750-mile (~1,207-kilometer) journey to Las Vegas, NV. It is a fairly direct route taking I-70 westward into Utah and then turning south on I-15 to Las Vegas. What can you say about I-70 in Colorado except spectacular! Driving through the canyons on the way to Grand Junction cannot be described but must be experienced. The greenery, rock formations, winding rivers, and lodges are exactly like you would imagine in storybooks. I can see what the challenges might be trying to navigate this interstate in the winter.
Heading into Utah was also quite interesting. Like Minnesota and South Dakota, the interstate seemed to go on forever. The scenery was unbelievable with tons of flat land but areas of majestic mountains that went on and on. A word of caution to those doing this drive. Pay attention to your gas gage! There are not many exits with gas stations. While the exit sign said gas this exit, the arrow said 20 miles [32.2 kilometers] into the desert. No thanks! Back on the highway to Las Vegas.
After a grueling day of driving, I am calling it a night just north of Las Vegas. I could tell that “Concrete Connie" and her sisters were exhausted too because the expressions on their faces had not changed since we left Denver.
Fun Fact: Much of the concrete used in the production of the casino/hotels in Las Vegas contained an accelerating additive from Master Builders Solutions. These additives are typically used to decrease the setting time and increase the early strength of concrete placed in cold weather. The reason the accelerating additive was used in this hot desert environment was that the economic models showed a significant loss of revenue for every day the casino was not open. The construction schedules were hastened using high early-strength concrete to complete the projects quicker.
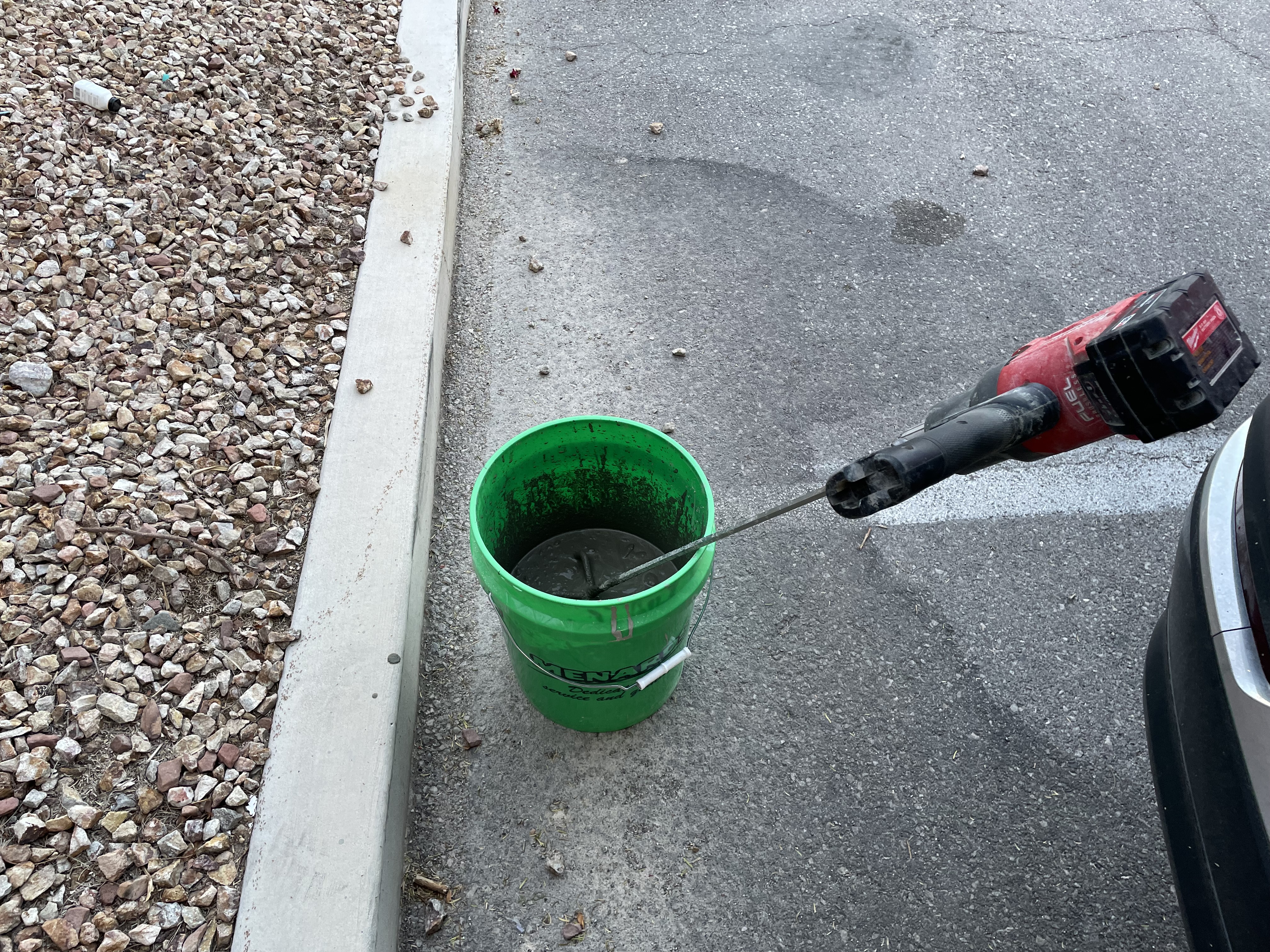
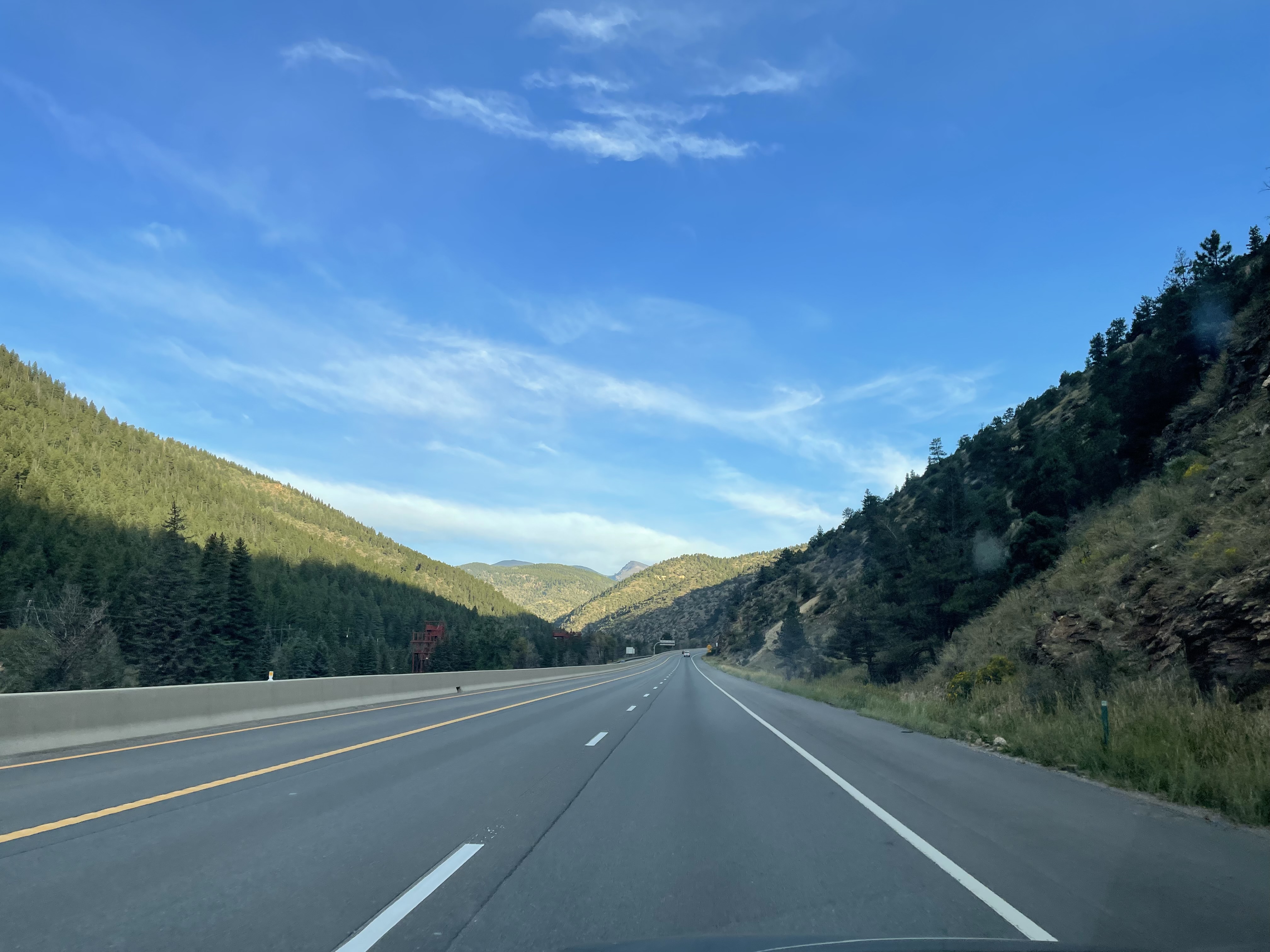
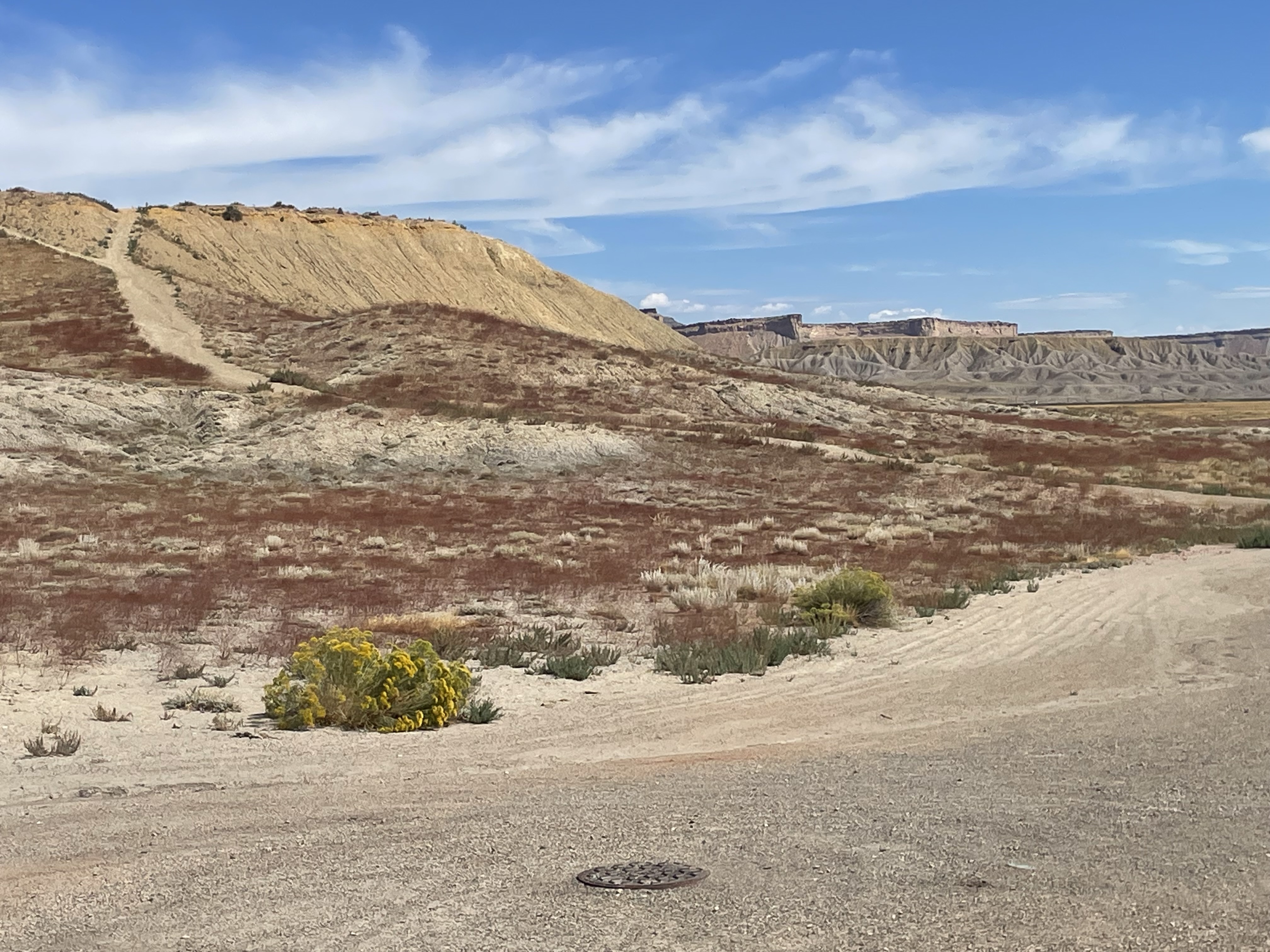
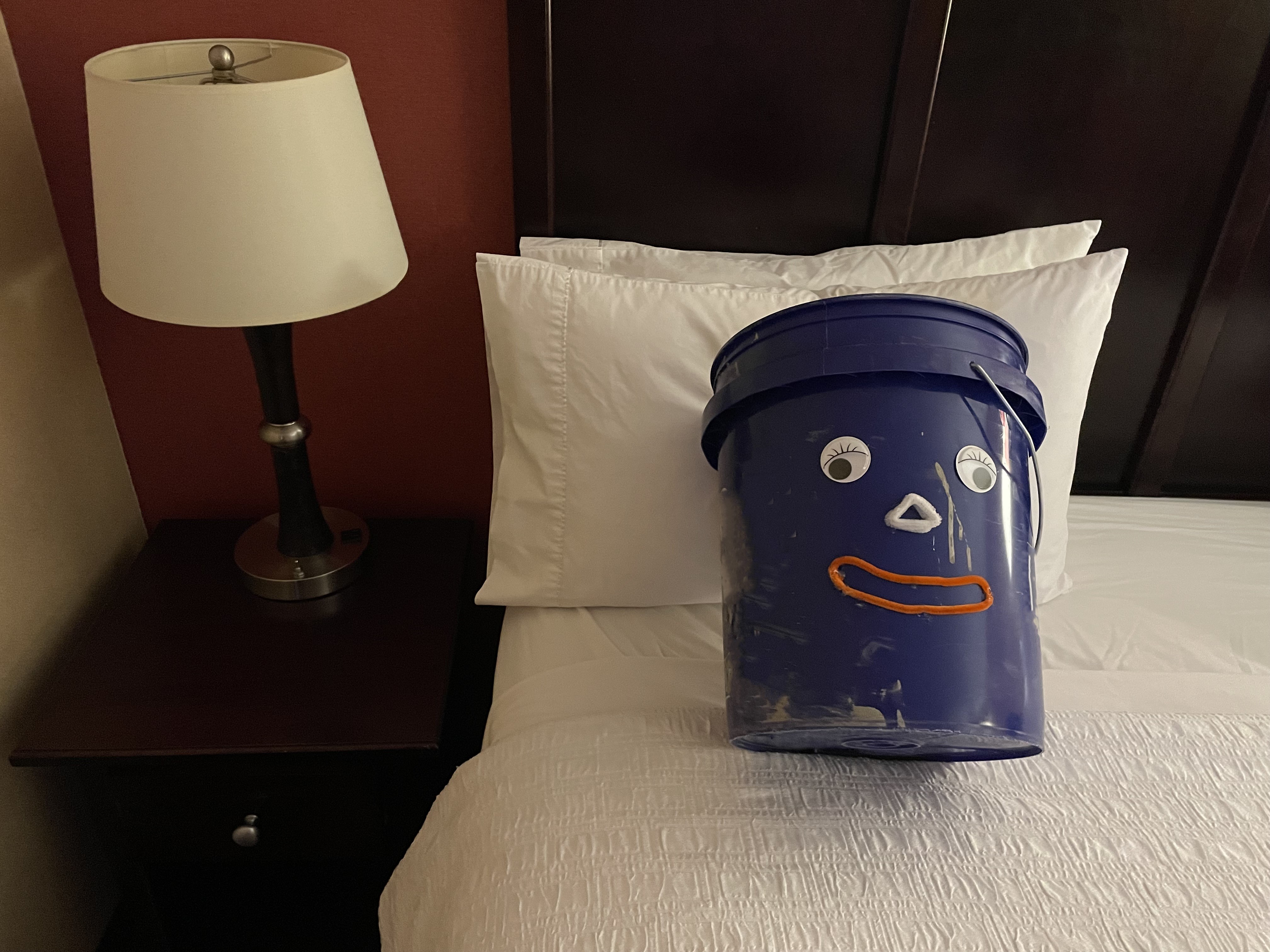
Day 7
Entering the final day of the journey to California was exciting for several reasons. First, it would be the last day of significant driving and secondly, I am making a stop at a historic landmark for the concrete industry, the Hoover Dam. I arrived at the Hoover Dam before it was officially open but wanted to get some photos before proceeding on to San Francisco. Similar to seeing the other amazing sights, my reaction to this one in person was “Dam(n), that's a lot of concrete!"
The remainder of the day was spent driving through the hot desert until arriving in San Francisco where the temp was 65 OF (18.3 OC).. I snapped a picture of the Golden Gate Bridge, barely visible through the fog and then turned towards the hotel fighting the sunset but not before mxing the concrete, which remained plastic now for 7 days.
Fun Fact: Construction of the Hoover Dam in the early 1930’s utilized the first water-reducing admixture from Master Builders Solutions, now MasterPozzolith®, to help facilitate placement.
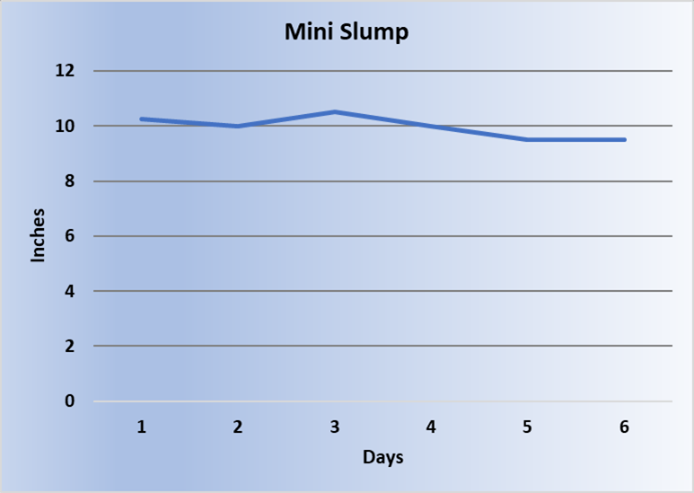
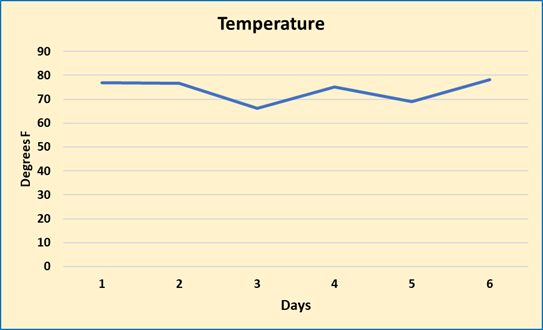
Day 8
5:00 am, the alarm sounded signifying the start of another day in the life of the now famous concrete from Maine. After a week of driving, the end of the trip was in sight. Was the concrete going to remain fluid? After giving the buckets of concrete a stir, fluidity was confirmed! Central Concrete, a subsidiary of Vulcan Materials Company, a Master Builders Solutions customer who produces high quality concrete with a focus on sustainability, graciously agreed to help us test the week-old concrete by mixing and blending it with fresh concrete in their laboratory. Over 50 test specimens were cast at the Vulcan National Research Laboratory in San Jose.
The idea of this trip, beyond my desire to complete a cross country trip, was to continue to promote a zero-waste concept for concrete and share the possibilities and opportunities afforded by admixtures.
By using the MasterSet DELVO hydration stabilizer, extra concrete left over from a project can be kept fresh, typically for a few hours or overnight, to be combined (recycled) later with newly batched concrete for use in a project, thereby minimizing waste. This practice is described in ASTM C1798/C1798M – 19 Standard Specification for Returned Fresh Concrete for use in a New Batch of Ready-Mixed Concrete. In this case, we kept it fresh for 7 days to emphasize the point of having total control of concrete setting, which is an important performance parameter for contractors placing concrete.
MasterSet DELVO - For information on stabilizing returned plastic concrete for recycling by blending the stabilized concrete with fresh concrete for reuse the same day or the following day.
Another option for recycling returned concrete is to treat it with a technology called MasterSuna® RCT 323 admixture for returned concrete. This admixture is mixed with returned fluid concrete to convert it into a granular material that can later be used as road bed, clean fill, or recycled back into making fresh concrete as a portion of the aggregate. The testing after this trip was the first time stabilized 7-day old fluid concrete was evaluated with MasterSuna RCT 323 admixture and it successfully transformed the fluid concrete into a granular material in less than 30 seconds. Score another point for concrete sustainability!
MasterSuna RCT 323 - For information on a sustainable engineered powdered admixture that gels returned fresh concrete resulting in very rapid stiffening, significantly minimized cement hydration and strength development. The end product is a recycled hardened granular material that can be used as a road bed, fill material, or for use in other applications.
Fun Fact: Everyone can participate in reductions in concrete CO2 by either method of recycling returned fresh concrete, regardless of the magnitude of annual production.
During this trip, we kept concrete fresh for 7 days to emphasize the point of being able to control concrete setting using admixtures even though it is highly unlikely that you would require this level of control in practice. Concrete setting time is an important performance parameter for contractors placing concrete. Master Builders Solutions has a portfolio of retarders, accelerators, hydration stabilization, and recycling admixtures to help the industry ensure sustainable, quality construction using concrete.
What an adventure! I drove through 17 states through all kinds of weather, although much of it was in the 90's. It gave me a real appreciation for how big this country is. I'm certain a world record was achieved in keeping concrete fresh for 7 days and transporting it over 4,200 miles (6,759 kilometers) for reuse and testing purposes (even if it's not official).
So tomorrow, I will be flying home, getting some rest, and then figuring out the next cool adventure to start planning.